The core technical logic of industrial sliding door installation.
The installation of industrial sliding doors is a systematic engineering process that demands careful consideration of mechanical structure, precision, and safety. Its core logic lies in integrating components such as door panels, tracks, and drive systems into a stable whole through scientific steps, ensuring the door operates efficiently and safely under frequent use. Key challenges in installation include:
Mechanical Matching Between Tracks and Walls
Tracks must bear the weight of the door and operational impact forces. During installation, precise calibration of horizontal and vertical alignment is essential to avoid door jamming or deformation caused by uneven stress.
Tension Adjustment of the Spring System
Sliding doors rely on springs to balance the door’s weight. Excessive tension accelerates component wear, while insufficient tension causes the door to sag. Adjustments must be precise to the millimeter level.
Integration of Motors and Control Systems
Motor power, limit switches, and door weight must be matched to ensure stable opening/closing speeds and overload protection functionality.
Pre-Installation Preparation
Measure the dimensions of the door opening and confirm the wall structure (concrete, steel structure, etc.) to formulate a fixing plan using expansion bolts or welding.
Inspect the integrity of door components and clear obstacles at the installation site.
Track Installation
Use a laser level to calibrate the tracks, ensuring left and right tracks are parallel and perpendicular to the ground.
Secure track brackets with high-strength expansion bolts or welding, with bolt spacing complying with manufacturer specifications (typically ≤500mm).
Door Panel Assembly and Hoisting
Spring System Debugging
Gradually stretch the springs while monitoring tension with a tensiometer to maintain door balance at any position.
Install safety ropes or anti-break devices to prevent accidents caused by spring failure.
Motor and Control System Installation
Fix the motor in the designated position, connect power and control lines, and test forward/backward functions.
Adjust limit switches to ensure the door stops automatically when fully open/closed, with an error margin ≤5mm.
Overall Testing and Acceptance
Conduct 5–10 opening/closing tests to check for operational noise (typically ≤60dB), jamming, and sealing performance.
Verify the strength of track fixation, door panel flatness, and the effectiveness of safety devices.
Prefabricated Module Assembly
Simplified Debugging Process
Employ an intelligent tension adjustment system that automatically matches spring tension via sensors, reducing debugging time.
Motors integrate one-click calibration functions, allowing the control system to auto-learn door weight and operational parameters.
Plug-and-Play Acceptance
Rail Installation Deviation
Issue: Unlevel tracks cause door misalignment.
Solution: Use a high-precision laser level for calibration, fix brackets in stages, and repeatedly measure alignment.
Spring Tension Imbalance
Issue: jamming or self-lowering during door operation.
Solution: Conduct debugging with two operators, gradually adjusting springs and verifying balance through door equilibrium tests.
Motor-Door Mismatch
Issue: Insufficient motor power leads to slow operation or overload tripping.
Solution: Select an appropriately sized motor based on door weight and dimensions before installation, In the context of the sentence 10%–20% power redundancy.
Safety Hazard Prevention
Regular Lubrication: Apply industrial lubricant to tracks, hinges, and springs monthly to reduce wear.
Sensor Calibration: Inspect the sensitivity of infrared sensors and limit switches quarterly to ensure accurate signal transmission.
Structural Inspection: Have professionals annually check for loose track bolts and door panel deformation, replacing aged components promptly.
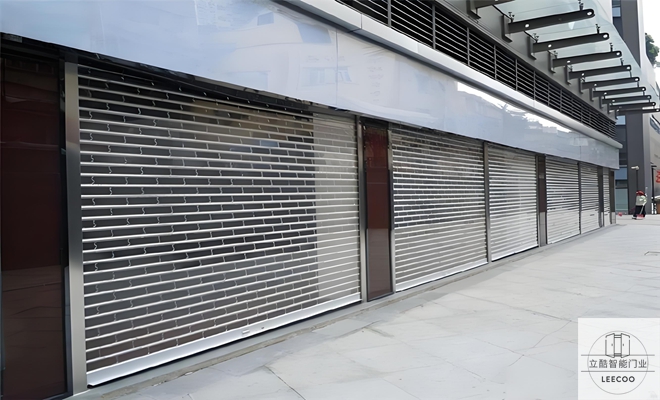
The installation quality of industrial sliding doors directly impacts their service life and safety. Whether using standardized processes or modular rapid installation, the key lies in strictly adhering to technical specifications and paying meticulous attention to debugging. For large projects or complex scenarios, engaging experienced professional teams is recommended to ensure the door meets design standards and provides reliable access security for industrial facilities.